We use cookies on our website. By continuing to use this site, you agree to our Cookie Policy
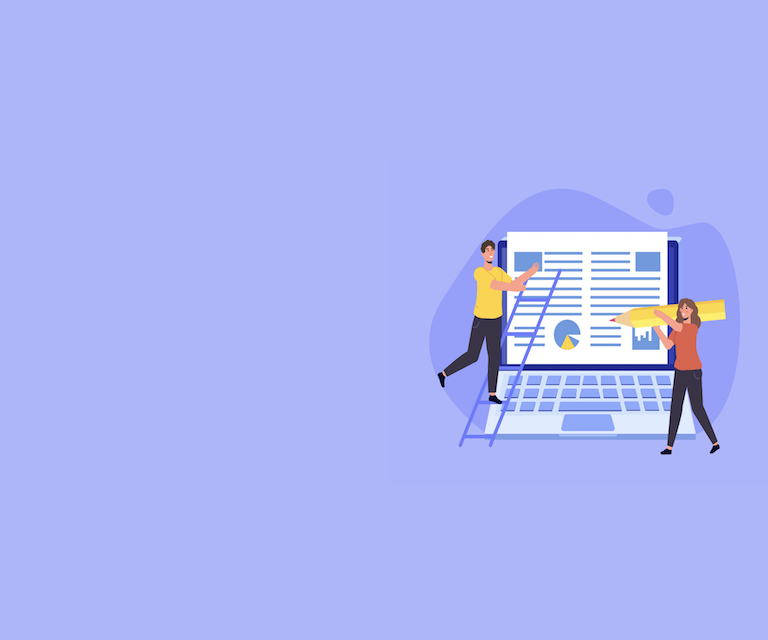
Transforming Digital Backbone for the ‘Brilliant Factory’ Program for a Fortune 20 Global Conglomerate across 18 countries
Microland has been the services partner designing, building, and managing their network infrastructure for over two decades. The customer naturally trusted our technical expertise, ability to deliver globally based on our track record.
During the transformation, Microland discovered several challenges such as
- Lack of information about OT devices and its TCP-IP communication flow
- Complexity in establishing connectivity to critical devices considering the size of sites
- Dealing with legacy machines that are resistant to changes due to protocol incompatibilities
- Security risks when connecting systems that are running with legacy/non-standard software to the network
- The need for revalidating equipment after every single modification
- Dealing with extreme environments that requires suitable network gear
- Adhering to strict access policies and safety regulations
- Downtime approvals for maintenance because majority of factories operate 24*7, etc.
- In the customer’s factories, the IT & OT devices were run on isolated and independent networks, with entirely different objectives and requirements.
- The customer had little or no real-time visibility on the performance of machines and were reliant on manually collected data and tribal knowledge to make decisions.
- Without key information about machine performance, asset availability & productivity it meant longer cycle of forecasting, tracking and decision making etc. Not only did the customer saw the need to modernize their industrial network architecture to make their products more intelligent, but digitalization was also becoming increasingly common across manufacturers of components and systems.
Our Fortune 50 Customer is a global conglomerate which operates in various segments such as Aviation, Power, Healthcare, Renewable Energy, and Additive Manufacturing. The customer has over 500 Manufacturing sites among over 2000 sites spread across the globe with over 200,000 employees.
Microland has been the services partner designing, building, and managing their network infrastructure for over two decades. The customer naturally trusted our technical expertise, ability to deliver globally based on our track record.
Once the customer decided to invest in digital transformation, we collaborated with them on this initiative that was termed ‘Brilliant Factory’ or ‘Factories of the future’. The initiative had 3 clearly defined goals
- Get Connected - Establish a standardized infrastructure that converges IT & OT technologies.
- Get Insights - Leverage the converged architecture to collect, analyze and assess production information in near real-time.
- Get optimized - Leverage the acquired intelligence and insights to promote effective optimization of the business from innovation and design, through supply and manufacturing, to distribution and customer use.
Microland identified a team of industrial network experts who jointly worked with the client’s technology division to develop a converged IT/OT (information and Operational Technology) solution for their manufacturing sites. Keeping the primary goal of connectivity in mind, Industry 4.0 standard was adopted to enable digital transformation. The standard provided the framework to setup standardized, secure and resilient architecture.
We then piloted and tested newly developed solution at a few factories initially. The pilot process helped us to identify challenges, fine tune our technical and business processes for large scale roll out.
During the transformation, Microland discovered several challenges such as
- Lack of information about OT devices and its TCP-IP communication flow
- Complexity in establishing connectivity to critical devices considering the size of sites
- Dealing with legacy machines that are resistant to changes due to protocol incompatibilities
- Security risks when connecting systems that are running with legacy/non-standard software to the network
- The need for revalidating equipment after every single modification
- Dealing with extreme environments that requires suitable network gear
- Adhering to strict access policies and safety regulations
- Downtime approvals for maintenance because majority of factories operate 24*7, etc.
To address these challenges most effectively our team followed 4 steps approach: Discovery, Design, Build/Test and Release. Since 2017 our team has handled and delivered 100+ OT Network Design & Build projects across 18 countries.
We have helped our customer to connect thousands of industrial control system (ICS) devices such as sensors, PLCs, DCS, HMIs, SCADA systems, Kepware and historian etc. The network solution we provided consisted of WAN, Wired & Wireless LAN, Network Security for the entire manufacturing plant including their carpeted areas/offices along with providing a secured network medium for compute infrastructure where factory data/application are hosted/stored.
By successfully bridging the gap between the IT & OT technologies, Microland helped the customer achieve their vision of Brilliant Factory – Factory of the Future. The key benefits of the solution are:
- Decreased Cost of Quality through improved utilization of machines, tools, and people
- NPI Cycle time reduction by leveraging the acquired intelligence and insights for smart inventory management & automation of low value tasks
- Increased Overall Equipment Effectiveness (OEE) by reducing expensive unplanned downtime
- Increased Ontime Delivery (OTD) by linking real-time information back to the entire supply chain from supply through distribution, for timely/quick action and response
- Create a secure factory with end-to-end security built into the network, providing multiple layers of protection
The customer trusted us to deliver our solution in the World’s Largest Gas Turbine plant in the USA, that is up to 413 acres with 1.7 million square-foot of manufacturing space. As part of this project, we connected and tested over 1500 OT machines and 5000+ IT Endpoints.
More Customer Stories
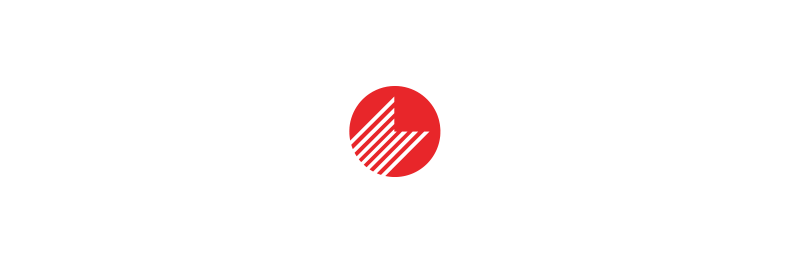

Please wait...
and we will be happy to help.